金属软管泄漏原因分析与预防
陈彩霞,王步美,陈杨
江苏省特种设备安全监督检验研究院


摘要:某核电设备上使用的金属软管在1年内发生泄漏。采用扫描电镜、光学显微镜、显微硬度计等仪器对泄漏的金属软管进行了宏观和微观检验、硬度检测及化学成分分析。结果表明,金属软管的泄漏是由钢丝网套与波纹管发生摩擦引起的机械损伤导致的。同时,提出了相应的预防措施。
关键词:金属软管;波纹管;钢丝网套;犁痕;摩擦
0引言
某主泵冷却水循环系统中使用的金属软管在1年内发生了泄漏,图1为使用单位采用气密性试验查找出泄漏部位、将该部位附近的钢丝网套去除后的金属软管的宏观形貌。该金属软管在使用现场竖直方向S形弯曲安装,两头法兰连接,通径DN80mm,长度750mm,现场有三维震动,有效振动加速度为水平2.1mm/s,垂直4.3mm/s,轴向8.5mm/s。工作压力12bar,工作温度75℃,介质为除盐水添加磷酸三钠,pH值11~11.5。
该金属软管按GB/T14525—2010《波纹金属软管通用技术条件》[1]生产制备。波纹管材料为06Cr18Ni11Ti,壁厚0.3mm,固溶热处理状态,材料标准为GB/T3280—2007《不锈钢冷轧钢板和钢带》[2];网套采用钢丝编织而成,编织参数为64mm×14mm×0.4mm,材料为06Cr19Ni10,冷拉状态,材料标准为GB/T4240—2009《不锈钢丝》[3]。
文中采用化学分析、硬度分析、宏观及微观检验等方法,对该金属软管的泄漏失效原因进行分析,并提出相应的预防措施。

图1泄漏金属软管宏观形貌
1理化检验
1.1宏观检验
1.1.1泄漏金属软管宏观形貌
图1示出泄漏金属软管及泄漏孔部位的宏观形貌,该金属软管略呈弯曲弧形状。泄漏孔位于波纹管波峰上,与波纹管的轴成45°,与外部网套的钢丝编织方向一致,在泄漏孔附近有很多与钢丝编织方向一致的磨痕,磨痕处呈黄褐色。泄漏孔附近的外部钢丝网套有黄褐色锈迹。
去除泄漏金属软管的钢丝网套,对钢丝网套内表面及波纹管进行宏观形貌观察。
钢丝网套内表面的宏观形貌如图2所示。可以看出,钢丝表面有锈迹,局部不平整,沿着钢丝的两个编织方向有钢丝凸出、翘曲现象。泄漏孔附近的钢丝网套内部的钢丝翘曲、凸出的程度更大,有的钢丝还发生错位折叠现象。将钢丝网套展开,在其内表面发现多处锈蚀部位存在磨痕。
波纹管的宏观形貌如图3所示。可以看出,金属软管整个波纹管段沿着轴向呈弯曲弧形状,泄漏孔位于波纹管背弯面一侧的波峰处。在泄漏孔附近的背弯面波峰上有许多磨痕,磨痕方向与波纹管轴向成45°,有的磨痕方向相互垂直,与外部钢丝网套的编织方向一致。



图2钢丝网套内表面宏观形貌
1.1.2波纹管泄漏孔、未磨穿磨痕、钢丝网套内表面磨痕宏观形貌
在图3所示的泄漏孔及未磨穿磨痕处分别取样,采用体式显微镜对其进行宏观检验。
泄漏孔的宏观形貌如图4所示。可以看出,泄漏孔外表面有黄褐色斑,局部有被磨蹭的白亮层,泄漏孔两头开口较大,沿着一定的倾角逐渐延伸至内表面;泄漏孔内表面周围区域光滑,在泄漏孔边缘连着一条未完全脱离的金属皮。

图3波纹管的宏观形貌



图4泄漏孔的宏观形貌
未磨穿磨痕的宏观形貌如图5所示。可以看出,磨痕位于波纹管波峰外表面,沿着与波纹管轴向成45°方向上呈凹坑状,凹坑内部有与磨痕形成方向垂直的细微痕迹。

图5未磨穿磨痕的宏观形貌50×
在图2(c)所示的钢丝内表面磨痕处取样,采用体式显微镜对其进行宏观形貌观察,从图6中可以发现钢丝内表面有一定的磨损,钢丝局部变形,呈扁平状。
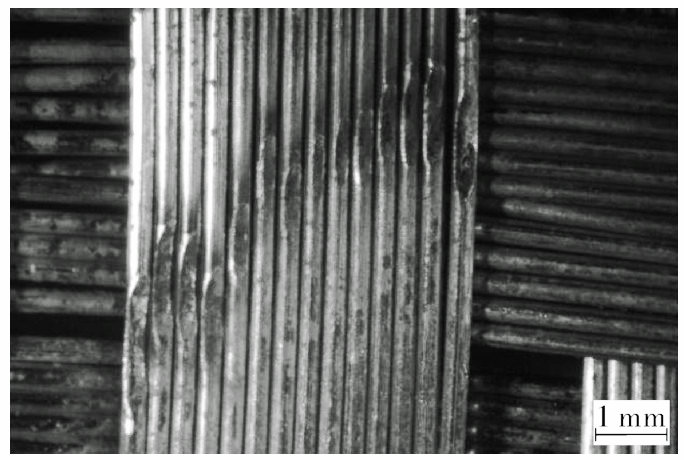
图6钢丝网套内表面磨痕宏观形貌10×
1.2化学成分分析
采用碳硫分析仪、电感耦合等离子体质谱仪、分光光度仪对波纹管、钢丝进行化学成分分析,结果如表1所示。

对照波纹管原材料标准GB/T3280—2007《不锈钢冷轧钢板和钢带》,其Cr,Ni,Ti含量偏低,但在GB/T222—2006《钢的成品化学成分允许偏差》范围内;对照钢丝原材料标准GB/T4240—2009《不锈钢丝》,钢丝的化学成分合格。
1.3波纹管泄漏孔、未磨穿磨痕微观形貌
采用扫描电镜对图4所示的泄漏孔内外表面、图5所示的未磨穿磨痕进行微观形貌观察。
泄漏孔的内外表面的微观形貌如图7所示。

图7(a)示出泄漏孔外表面的磨损形貌,泄漏孔两头留下沿着一个方向倾斜的条带,条带细窄且密集分布,将条带放大至500倍可见一条条的犁痕及深浅不一的犁沟,属典型的机械损伤形貌[4-5]。
整个泄漏部位内表面周围比较光滑,泄漏孔上面连着一条未完全撕裂的金属皮,上面布满纵向的条带,其方向与外表面两头区域的条带方向一致。泄漏孔边缘金属向内表面翘起。

图8未磨穿磨痕微观形貌
未磨穿磨痕的微观形貌如图8所示,磨痕内部有断续状的细微弧形台阶,呈鱼鳞状,是在磨痕形成过程中沿着磨痕形成方向及与磨痕形成方向垂直的两个方向逐渐挤压堆积而成的痕迹。
1.4能谱分析
对泄漏孔附近内外表面、未磨穿磨痕进行能谱分析。泄漏孔内外表面的分析结果如图9及表2、图10及表3所示,在泄漏孔外表面的磨痕头部(谱图3)有大量氧元素存在,外表面有少量氟、硫腐蚀性元素存在,泄漏孔内表面有少量氟元素。未磨穿磨痕的分析结果如图11及表4所示,磨痕内部有大量氧元素存在。可见波纹管外表面的氧、氟元素的含量高于其内表面相应元素的含量。

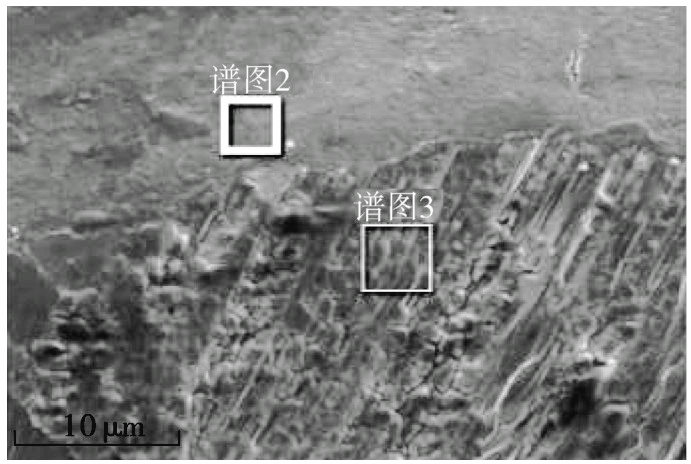
图9泄漏孔外表面
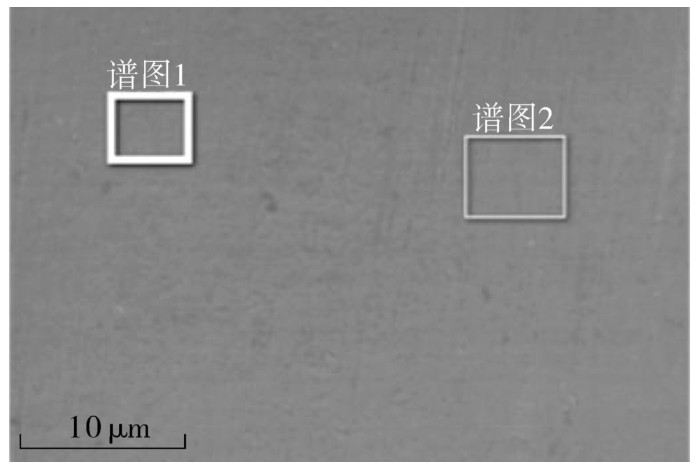
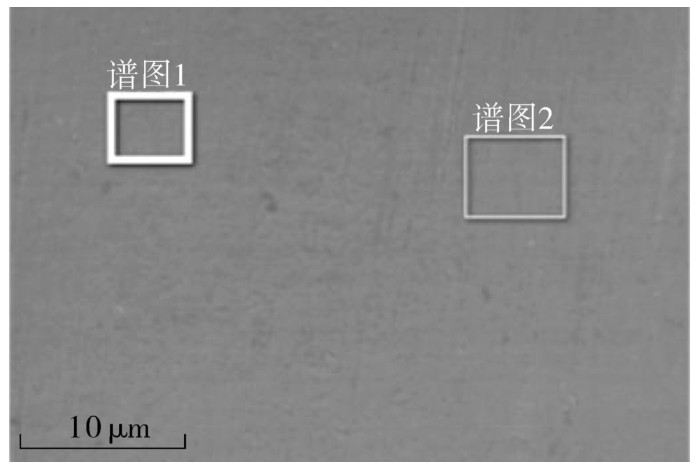
图10泄漏孔内表面


图11未磨穿磨痕处
1.5硬度分析
在波纹管磨痕处截取波峰横截面试样、波谷横截面试样,在钢丝网套上随机截取7根钢丝。在热镶嵌磨抛后进行显微维氏硬度试验(HV0.05),结果如表5所示,波纹管的硬度比钢丝的硬度低。

1.6金相组织



图12波纹管的金相组织200×
波峰横截面、表面金相组织和波谷横截面组织如图12所示,均为典型的奥氏体组织,晶内有挛晶。在金相组织中发现少量氮化物夹杂。
2 分析与讨论该金属软管的波纹管壁厚极薄(0.3mm),在三维振动的环境下使用了一年发生泄漏。经检验后发现泄漏金属软管的波纹管呈弯曲弧形状,在波纹管的背弯面一侧的波峰外表面处发现泄漏孔,泄漏孔附近的背弯面多处发现磨痕,其方向均与外表面的网套编织的两个垂直的方向一致;钢丝网套内表面有凸出、翘曲及错排等不平整现象,且钢丝内表面局部有一定的磨损,呈扁平状。
泄漏孔外表面存在被磨蹭的白亮层,两头开口较大,沿着一定的倾角逐渐延伸至内表面,边缘金属向内表面翘曲。泄漏孔外表面边缘处与内表面残留金属皮的微观形貌一致,为典型的犁痕形貌,属机械损伤。波纹管的未磨穿磨痕的微观形貌呈鱼鳞状,有细微弧形台阶,是在磨痕形成过程中沿着磨痕形成方向及与磨痕形成方向垂直的两个方向逐渐挤压堆积而成的痕迹。泄漏孔外表面的氧含量远大于内表面的含量,未磨穿磨痕处的氧含量也较高,可推断泄漏孔附近区域外表面的氧含量大于内表面的含量。波纹管的硬度低于钢丝的硬度。
综上所述,可推断泄漏金属软管在运行过程中,钢丝内表面与发生弯曲的波纹管发生相互摩擦,在波纹管波峰外表面留下摩擦磨痕,直至磨穿发生泄漏为止。泄漏金属软管的运行条件(三维有效振动加速度较低)、波纹管泄漏孔内外表面的微观形貌中发现典型的犁痕形貌、犁沟现象,未磨穿磨痕表面微观形貌中发现的挤压堆积痕迹,符合微动磨损的发生条件[4,6-8]。
3结语
该金属软管泄漏失效是由波纹管与钢丝网套摩擦导致的机械损伤。为了避免以后这类摩擦导致的磨损泄漏事故的再次产生,建议如下。
(1)优化金属软管的制造工艺,加强对钢丝网套的外观检验,避免出现网套表面不平整、断丝、折叠、凸出、翘曲等现象[1,7-8];
(2)改善金属软管的现场安装条件,应保证顺其自然直线安装,不应任意压缩弯曲呈“~”形安装[9-10]。
参考文献:
[1]GB/T14525—2010,波纹金属软管通用技术条件[S].
[2]GB/T3280—2007,不锈钢冷轧钢板和钢带[S].
[3]GB/T4240—2009,不锈钢丝[S].
[4]张栋,钟培道,陶春虎,等.失效分析[M].北京:国防工业出版社,2008:241-253.
[5]刘杰英.磨损失效分析案例汇编[M].北京:机械工业出版社,2005.
[6]徐松.金属材料磨损失效及防护的探讨[J].现代经济信息,2010(1):217.
[7]陈建敏,周惠娣.磨损失效与摩擦学新材料的研究与发展[J].材料保护,2004,37(7):35-39.
[8]杜健,李延夫,李晓旭,等.金属软管失效模式及失效原因分析[J].管道技术与设备,2015(3):1-3.
[9]齐艳丽,袁夕君,张金平,等.核电厂设备冷却水系统金属软管使用中存在的问题及对策研究[J].机械,2012(9):73-77.
[10]郭兆海.石油储罐进出口管段用抗震金属软管[J].管道技术与设备,1998(2):30-32.
收稿日期:2017-11-01修稿日期:2018-01-25
作者简介:陈彩霞(1981—),女,高级工程师,主要从事理化检测和失效分析工作,通信地址:211178江苏省南京市江宁滨江经济开发区喜燕路18号,E-mail:jenifer0108@163.com。
► 如果本文对您有帮助,请分享给您的朋友!
【提示】:
1.不断更新的好资料和答疑集锦在 www.hb-qg.com “找资料”栏目公布。
2.QQ群:2300+人群,专业高质、答疑解惑、互动交流,Q群名:中国设备管理, Q群号: 283752911
主要交流:设备管理体系标准、ISO55001资产管理、设备完整性管理、6S管理、目视管理、安全管理、企业管理等,纯广告者禁入!
3.加"中国设备管理" Q群,总有一个人知道你问题的答案!
4.优秀留言有机会录入“找资料”栏目答疑集锦,并欢迎大家来稿分享